Usually, in the case of not fully automatic production, it is necessary to rely on manpower for assistance. Since the production process involves human factors, there must be differences in each production cycle, resulting in varying degrees of difference in the quality of parts. Especially in enterprises that implement three-shift production, the quality of parts produced by different shifts is quite different, which is due to the different personal skills and work attitudes of operators in different shifts. Central conveying system can effectively avoid this phenomenon, and the equipment will follow the input instructions for production.
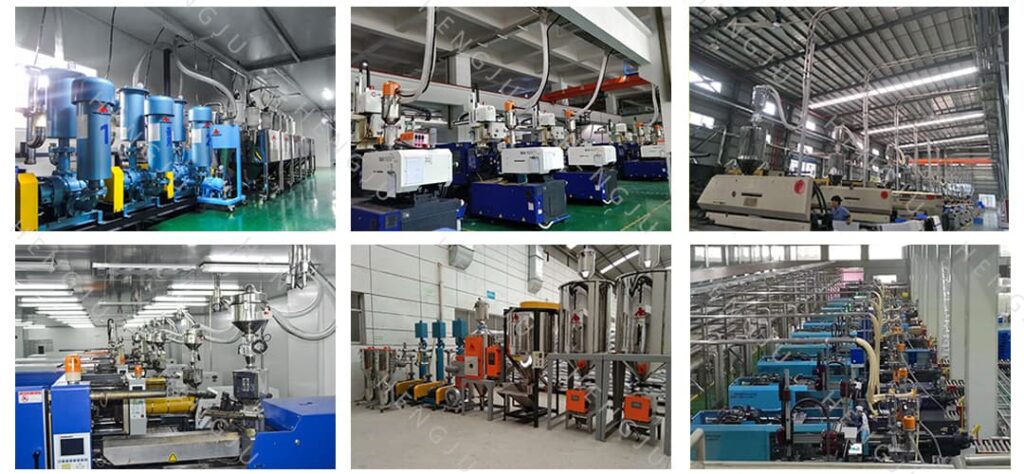
Central conveying system can stabilize the cycle, reduce the factors of human downtime, and significantly improve production efficiency. The centralized feeding system uses pneumatic conveying to transport bagged or bulk plastic granules to the silo for storage, and then the silo is sent to the drying system for drying treatment, and finally distributed to each injection mold by the central switching device through the pipeline. At the same time, the gate waste is collected and crushed by the automatic recycling system for recycling.
Advantages of central feeding system
1. Realized unmanned continuous molding operation all day.
2. Able to regenerate and use gate recycled materials in a fully automatic manner.
3. The combined use of the injection machine and multi-variety and multi-color materials can be changed according to the needs, so as to automate the coloring.
4. Through computer center monitoring, it saves labor and time, improves production efficiency and saves energy.
The centralized feeding system overcomes the labor-intensive and time-consuming disadvantages of single-machine operation in the past. For injection molding parts produced by multiple machines and in large quantities, the economic benefits are significant.