There are several common appearance defects that can occur in injection molding plastic products:
Sink marks: Sink marks are depressions or indentations on the surface of the plastic part caused by uneven cooling or insufficient packing of the material.
Flash: Flash is the excess material that protrudes from the parting line of the mold, usually caused by improper clamping force or excessive injection pressure.
Burn marks: Burn marks are discoloration or dark spots on the surface of the part caused by excessive heat during the injection molding process.
Gate marks: Gate marks are small marks or scars left on the surface of the part where the plastic material enters the mold cavity through the gate.
To minimize these appearance defects, it is important to optimize the injection molding process parameters, ensure proper mold design and maintenance, use high-quality materials, and conduct regular inspections and quality control measures.
The use of injection molding plastic auxiliary equipment can help address some of the common appearance defects in injection molded plastic products. Here are a few examples:
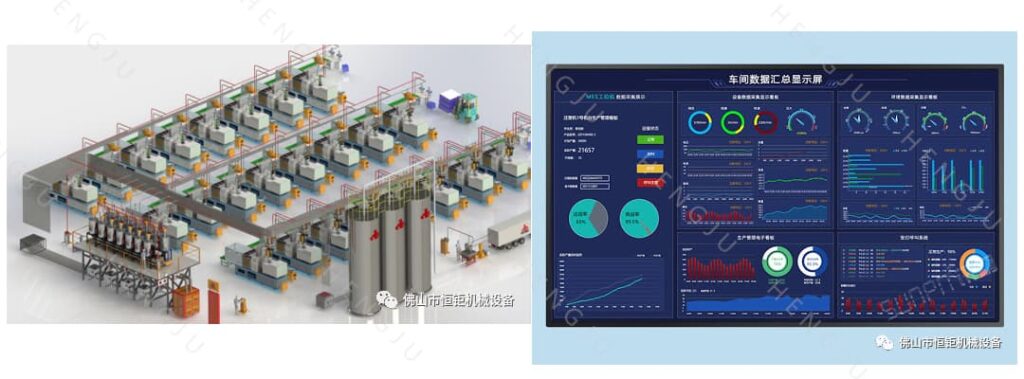
Mold temperature controllers: By precisely controlling the mold temperature, mold temperature controllers can help reduce or eliminate sink marks and flow marks by ensuring uniform cooling of the plastic material.
Plastic hopper dryers: Moisture in plastic materials can cause surface defects such as bubbles or voids. Plastic hopper dryers remove moisture from the plastic pellets before they are processed, reducing the likelihood of these defects.
Volumetric mixers: Inconsistent material mixing can lead to variations in color or composition, resulting in visual defects. Volumetric mixers ensure thorough blending of additives and colorants, promoting uniformity in the final product.
Central conveying systems: Central conveying systems can detect abnormalities in the injection molding process, such as excessive pressure or temperature, and alert operators to take corrective actions promptly, preventing defects from occurring.
By incorporating appropriate plastic auxiliary equipment into the injection molding process, manufacturers can enhance product quality, improve efficiency, and reduce the occurrence of appearance defects in plastic products.