In the fast-paced world of injection molding, efficiency and precision are paramount. Auto hopper loaders have emerged as indispensable tools in this industry, revolutionizing material handling processes and ensuring uninterrupted production. This article explores the innovative applications and transformative impact of auto hopper loaders in injection molding, highlighting their crucial role in driving productivity and minimizing downtime.
Unveiling Auto Hopper Loaders
Auto hopper loaders represent a breakthrough in material handling technology. These automated systems are designed to transport plastic resin materials from storage containers to injection molding machines with precision and efficiency. Utilizing advanced mechanisms such as vacuum suction or mechanical conveying, they streamline material logistics, eliminating manual intervention and optimizing production workflows.
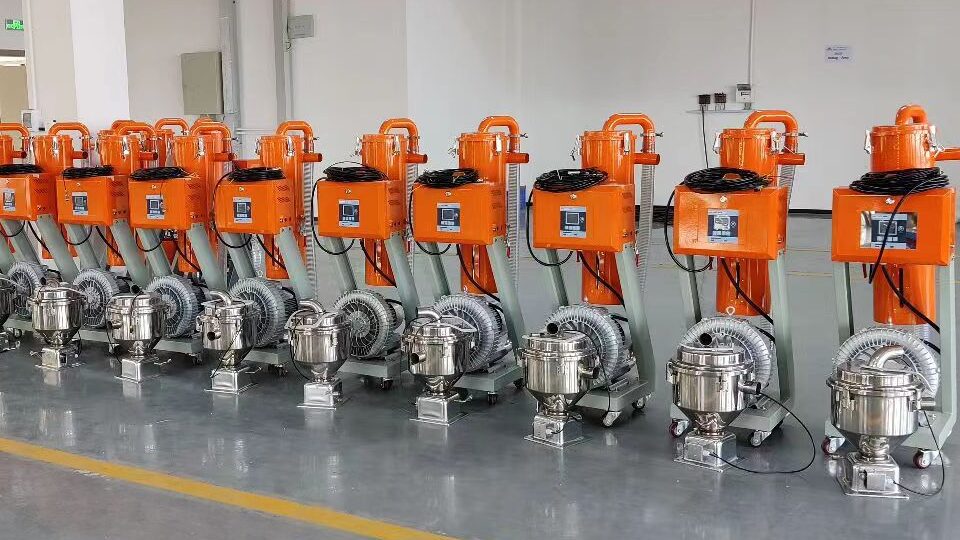
Advantages Redefining Injection Molding
- Seamless Material Handling
- Auto hopper loaders ensure a continuous supply of plastic resin materials to injection molding machines, minimizing downtime and optimizing production throughput.
- Precision and Consistency
- With precise control over material transfer, these loaders guarantee consistent resin feed rates, resulting in uniform product quality and reduced scrap rates.
- Cost Savings and Efficiency
- By automating material loading tasks, auto hopper loaders reduce labor costs and minimize material waste, leading to improved profitability and operational efficiency.
- Enhanced Workflow Integration
- These loaders seamlessly integrate into injection molding setups, enhancing workflow continuity and facilitating smoother material logistics from storage to processing stages.
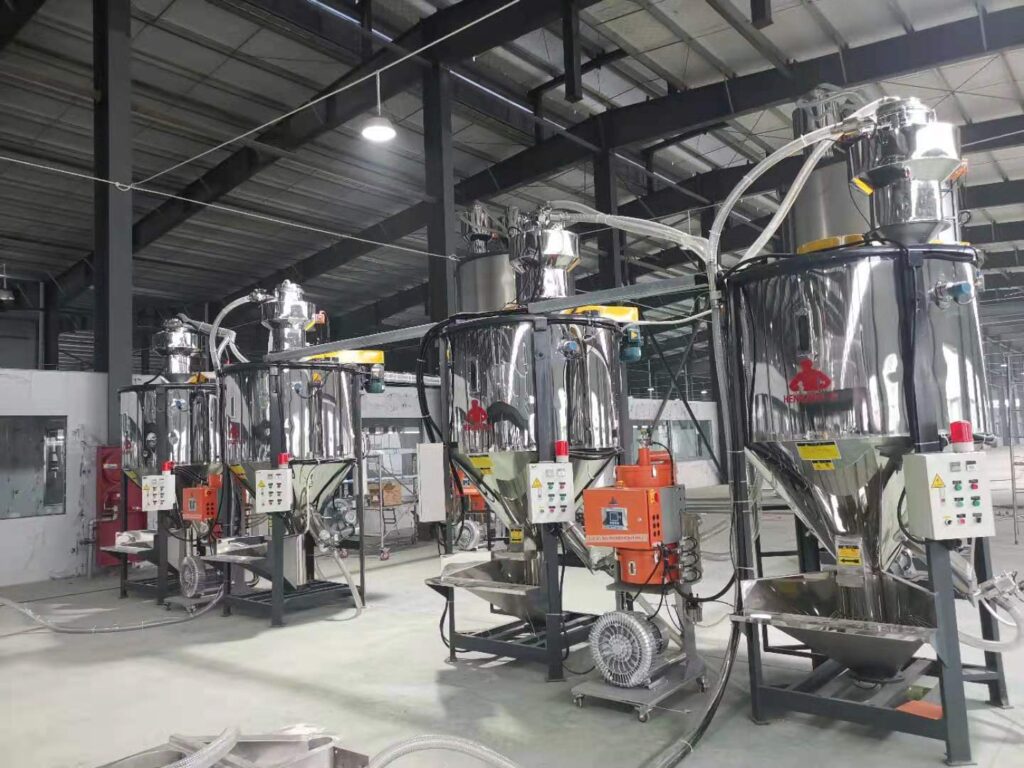
Applications in Injection Molding
1. Continuous Production
- Auto hopper loaders enable injection molding machines to operate continuously by ensuring a steady supply of resin materials, maximizing production output and minimizing downtime.
2. Material Flexibility
- These loaders are compatible with a wide range of plastic resins, allowing injection molders to switch between materials easily and adapt to changing production requirements.
3. Quality Assurance
- By delivering resin materials with precision and consistency, auto hopper loaders contribute to the production of high-quality injection molded parts with minimal defects or variations.
4. Streamlined Setup Changes
- Auto hopper loaders facilitate quick and efficient material changes, reducing setup times and improving overall production efficiency in injection molding facilities.
Conclusion
Auto hopper loaders have become indispensable assets in injection molding operations, empowering manufacturers to achieve higher levels of efficiency, productivity, and product quality. Their ability to streamline material handling processes, minimize downtime, and optimize resin utilization makes them invaluable tools for injection molders seeking to stay competitive in today’s fast-paced market.