Central conveying system
Realize Enterprise Transformation Through Digital central material feeding system Upgrading.
There are a large number of plastic manufacturing enterprises in China, but the production process of plastic products is highly dependent on manual production mode. Problems such as labor cost, management cost, and mistakes made by employees in the production process have caused problems that restrict the development of enterprises, such as low product efficiency, insufficient anti-risk ability, and low gross profit margin of products.
Coupled with the rapid economic development, homogeneous products are dazzling, and consumers’ demand for quality is getting higher and higher. If we want to greatly improve product quality and production efficiency, reduce costs and increase efficiency, we can realize enterprise transformation and upgrading through digital upgrading.
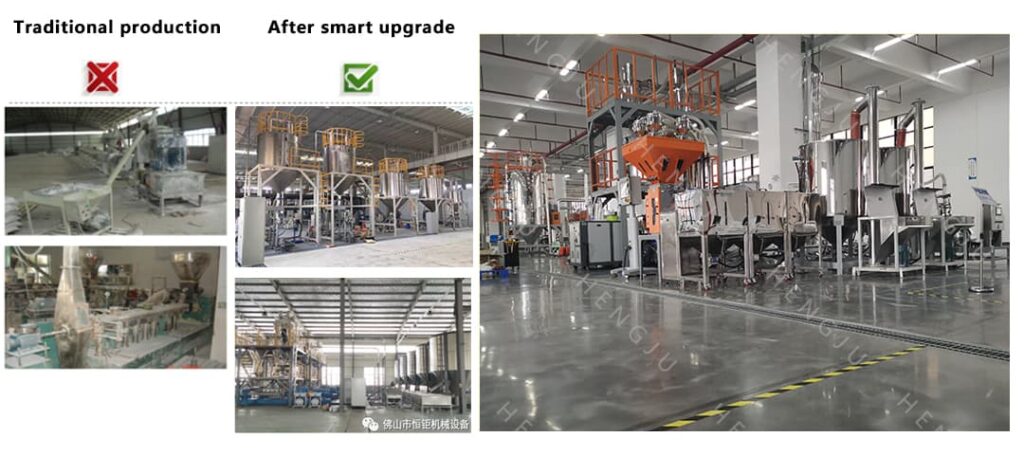
Three major problems of upgrading
Three major problems faced by digital and unmanned upgrading and transformation of plastic production enterprises
1. There is no relevant technical ability in the informatization of plastic production, and the enterprise relies on experienced employees, and the informatization talent pool is insufficient.
2. Problems such as employees’ mistakes in the production process, such as low product efficiency, insufficient ability to resist risks and low gross profit margin of products, restrict the development of enterprises.
3.The personnel cost is high, and the transportation cost is high. The profit growth of most manufacturing enterprises is declining, but the personnel cost has been rising.
How to solve the problem
Hengju Machinery actively responded to the national policy of strongly supporting the upgrading and transformation of plastic enterprises, and launched the “Empowering 100 Enterprises” plan of digitalization, intelligence and unmanned plastic manufacturing industry for plastic production enterprises, aiming at empowering 100 plastic production enterprises to quickly complete the digitalization, intelligence and unmanned upgrading and transformation of production workshops in the next three years.
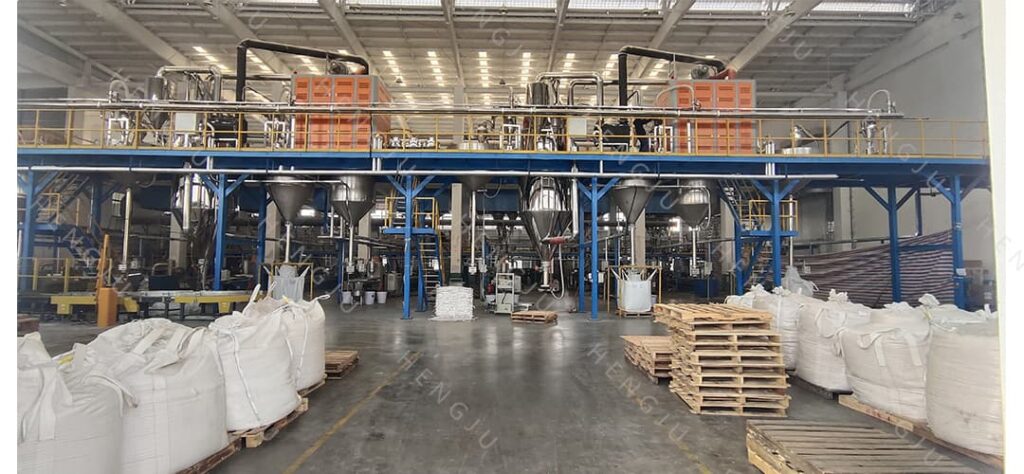
The central conveying system is designed for the production of plastic products in the injection workshop, which realizes uninterrupted unmanned continuous molding operation.
Production process data
The visualization of production data, such as material usage, product yield and equipment startup, is clear at a glance, and the system is easy to understand and operate.
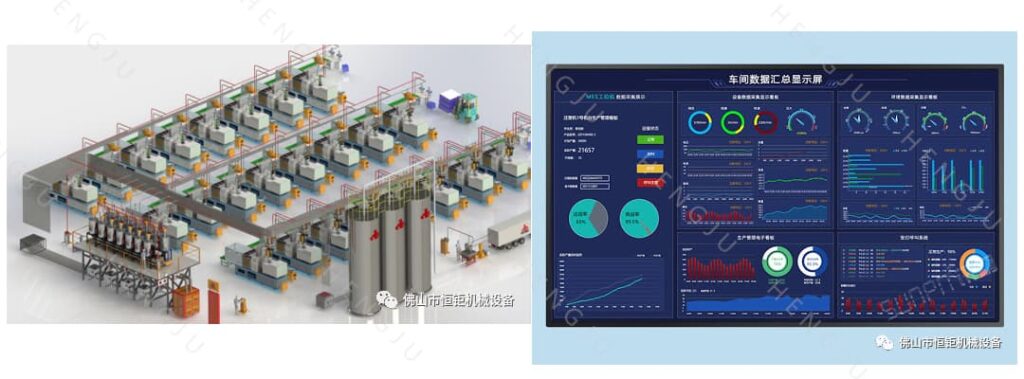
Enterprise image upgrading
The intelligent drying management system can automatically adjust the drying temperature by monitoring the consumption of raw materials, and automatically reduce the drying temperature when the consumption of raw materials is low to prevent damage to raw materials, which not only saves a lot of heat energy, but also ensures the continuity of production.
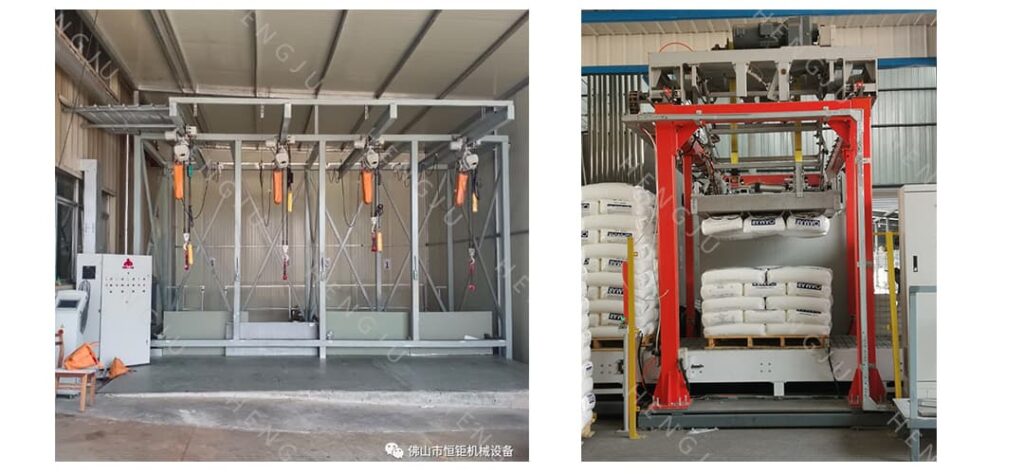
Intelligent transportation
Central material conveying system to release factory space and reduce transportation costs. We solve the problem from the source, and adopt the packaging method of automatic unpacking machine. Raw material suppliers provide bulk materials, and adopt the method of container unloading. Bulk materials are cheaper than packaging materials, and enterprises with large usage can save more than one million dollars a year by using bulk materials.
case sharing
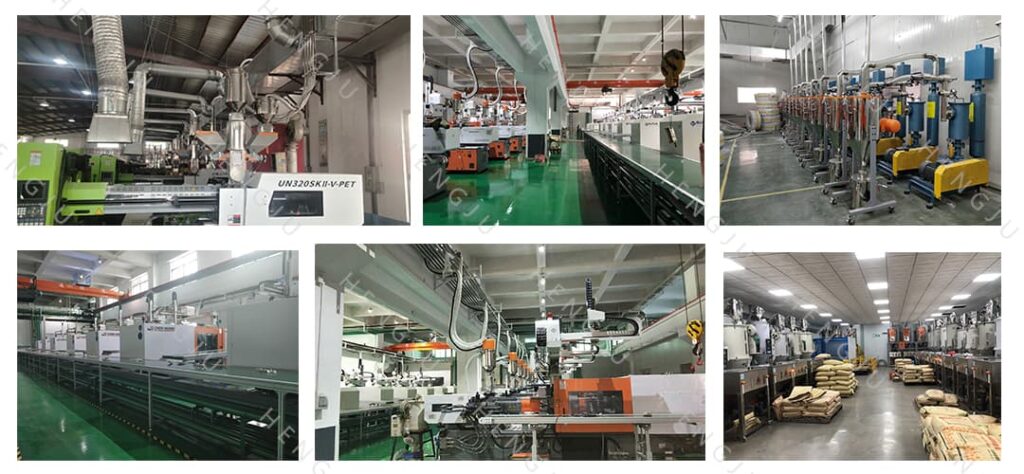
A household goods customer has 9 large storage bins of 125 cubic meters, with a loading capacity of 100T per hour, which greatly improves the storage capacity and quality.
The central conveying system can reduce the pollution of raw materials and dust to the lowest level, so as to keep the clean workshop standard, save energy and be efficient.
Realize the enterprise upgrade through digitalization and intelligence, and choose us to let you
Peace of mind: Our design scheme is tailor-made for the factory, with professional technology as the output scheme, and ensures the applicability of the planning.
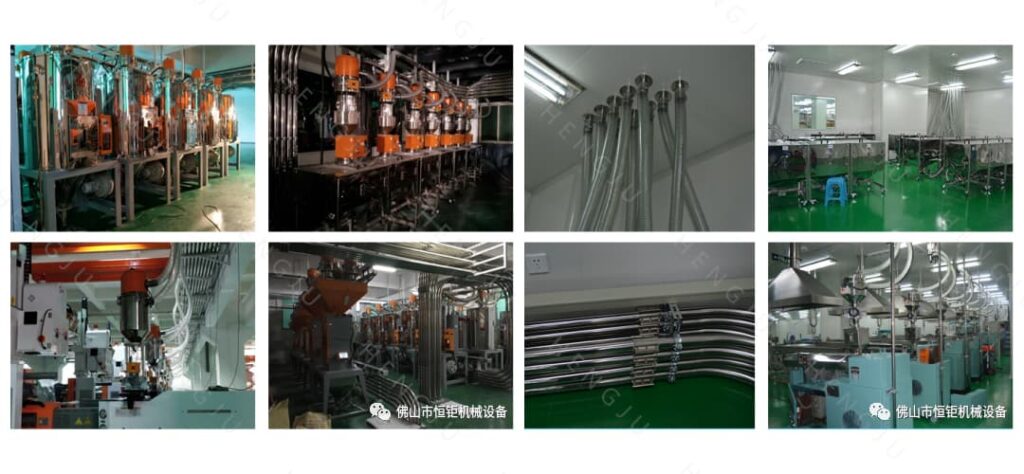
Worry-free: Our central conveying system is an intelligent interconnection mode. The incoming data, outgoing data, formula data and molding machine material consumption data are collected through data, and then transmitted to the ERP database to use the turnkey project of the whole system.
Rest assured: centralized feeding system all equipment is equipped with a set of professional and complete video for detailed explanation of use and maintenance, and a one-to-one follow-up service system is adopted after sales.
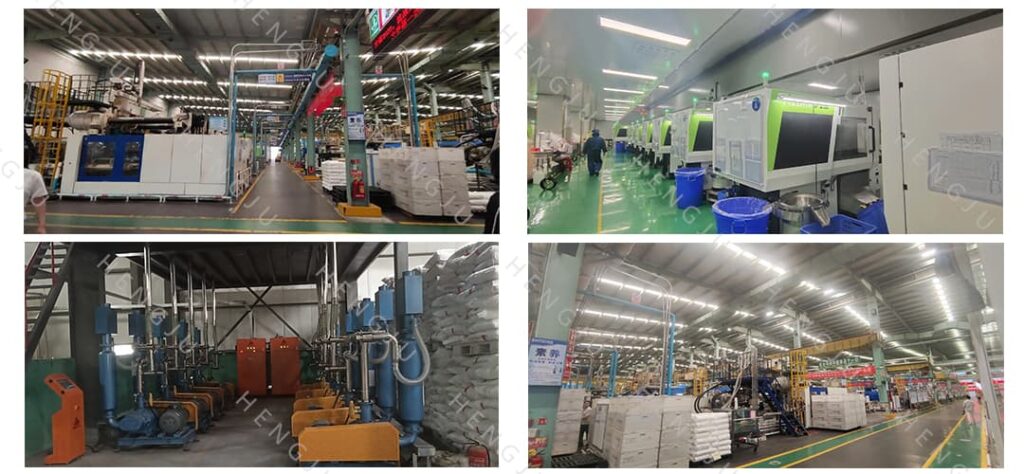
Focusing on customers’ concerns, we sincerely hope that we can work hand in hand with all industries in plastic production and seek common development.