For manufacturers who produce large-scale pipe or profile extrusion, the raw materials required for production are not only large in quantity but also of various types. In addition, the remaining area after placing production equipment in the factory area is small, and the placement of raw materials takes up a lot of space, resulting in high storage costs. Raw materials cannot be managed centrally. Traditional manual feeding is prone to errors and cannot be loaded in time, and it will lead to waste of raw materials and dust pollution in the workshop during the process of feeding, mixing ingredients, and handling, which can no longer meet the needs of current automated production.
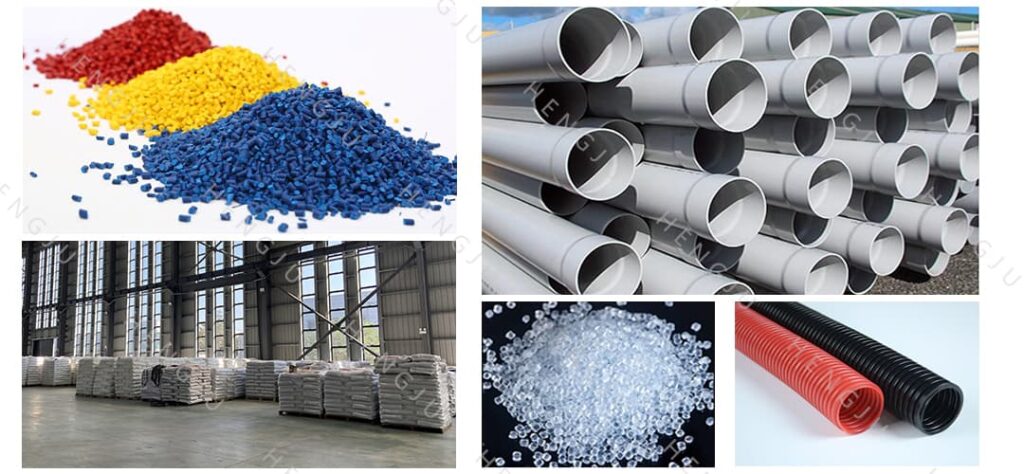
Outdoor silos and central conveying system realize automation and intelligence in the process from storage, weighing, batching and mixing of plastic raw materials to centralized conveying silo storage and extruder production. This storage method can prevent raw materials from being affected by moisture. Pollution, factory storage problems are solved.
Outdoor Silo solve industry storage pain points
1. Raw material storage occupies a large area.
Use the outdoor space to store raw materials, maximize the effective use of space in the factory, save raw material storage space, and reduce the storage cost of the enterprise.
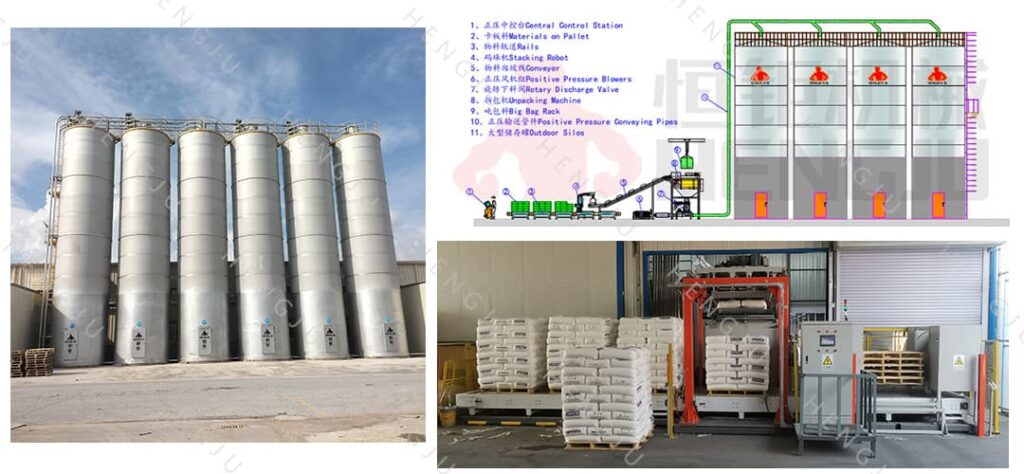
2. It takes a long time to store raw materials.
It supports code scanning to prevent raw materials from entering wrong positions, can effectively store and control raw materials, simplifies the workflow of raw material storage, and improves the management level of enterprise workshops.
3. Manual transportation is slow and costly.
Equipped with an automatic unpacking machine and a raw material conveying system by means of vacuum suction or blowing force, it saves labor costs and reduces transportation costs.
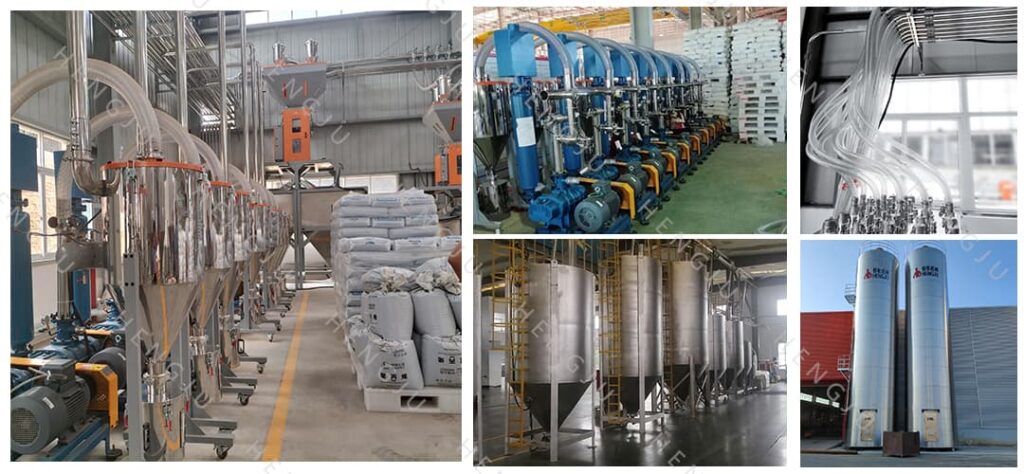
4. Raw materials are polluted and wasted, and the workshop environment is poor.
Centralized management of raw materials, stainless steel material and dust-free airtight pipe blowing to avoid raw material pollution and waste, improve the overall image of the company, and keep the factory environment clean.
How to break the flaws of traditional material supply, improve production efficiency and product qualification rate?
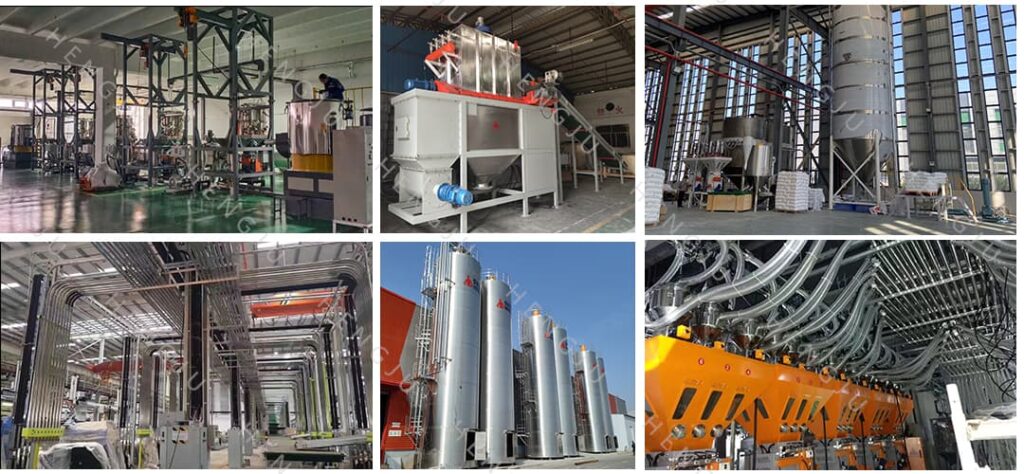
Since its establishment, Hengju Machinery has been focusing on the research and development of central conveying system, whole plant water and electricity planning, dehumidification and drying, and batching measurement, so as to make products closer to customer needs and customize perfect automation solutions for customers. From raw material storage, transportation, drying and dehumidification, weighing and measurement and other technological processes to realize production intelligence and automation upgrades, reduce costs and increase efficiency for enterprises, and enhance core competitiveness. We have provided stable and reliable intelligence for thousands of plastic manufacturers. system.
We will design and plan the optimal solution according to different plastic production workshops, according to different usage requirements and actual needs of different workshop characteristics, not only create safe working conditions for customers, reduce production costs, reduce energy consumption, but also Can create a good corporate image for the company.
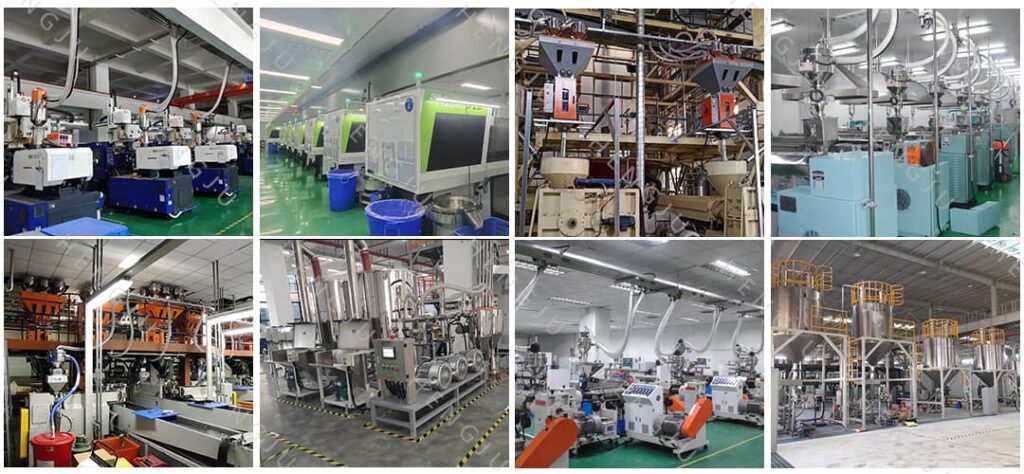